An in-house investigation team from Equinor has studied the deviation in quality of welding and inspection of the Johan Castberg production vessel currently under construction at the Sembcorp Marine yard in Singapore. Extensive work is being carried out to quality assure and cross-check welds and repair welding defects, to ensure that the vessel meets applicable safety and integrity requirements before leaving the yard.
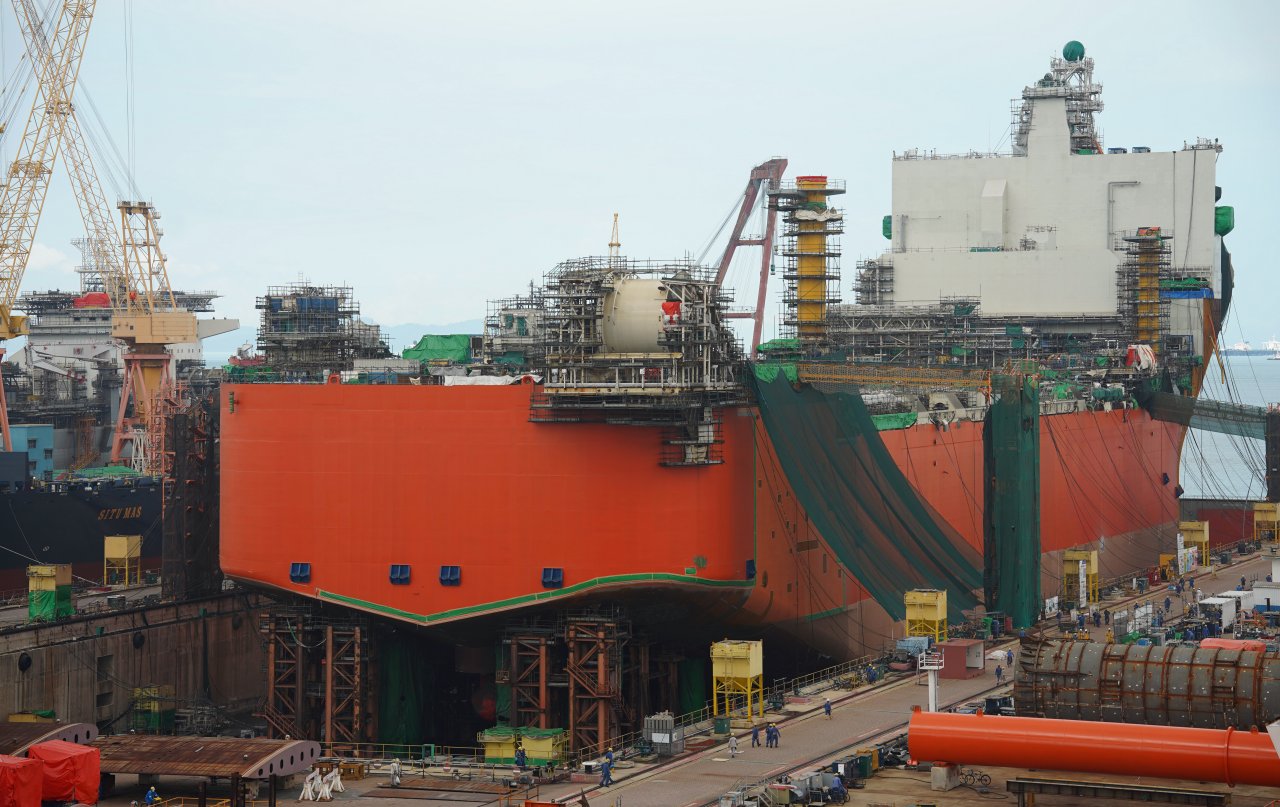
During construction of the hull for the Johan Castberg production vessel at Sembcorp Marine in Singapore, Equinor has revealed quality deviations regarding both welding and welding inspection.
“Safety is Equinor’s top priority. We are currently carrying out extensive cross-checking and repair of welds to ensure that the Johan Castberg production vessel meets the safety and integrity requirements. When Johan Castberg comes on stream, there should be no doubt that the vessel is safe,” says Geir Tungesvik, Equinor’s senior vice president for project development.
The yard is responsible for correcting all deviations in quality and costs related to repair of welding defects are covered by Sembcorp Marine, according to the contract. The cross-checks and improvements are almost completed and are followed up closely by Equinor.
“To ensure learning and avoid similar situations in other projects or at other yards, we have carried out a thorough investigation,” says Tungesvik.
The investigation team did not find any single event which can have been a direct cause for the welding quality issues, but have pointed out causal factors considered as having had an impact:
- Contractor (SCM) failed to provide sufficient competent welders and welding inspectors for execution of the scope and did not sufficiently comply with processes and work routines for execution and follow up of welding and inspection activities.
- Equinor has not sufficiently complied with its own work processes and procedures for risk management, construction management and follow-up at the construction site.
- Even if Equinor’s follow-up team found signs of poor quality at an early stage, the extent and degree of seriousness were not understood. Sufficient measures were therefore not implemented.
- Equinor’s follow-up team has not had enough personnel with experience and expertise in welding and welding control and has not utilized the company’s technical expertise in these areas early enough.
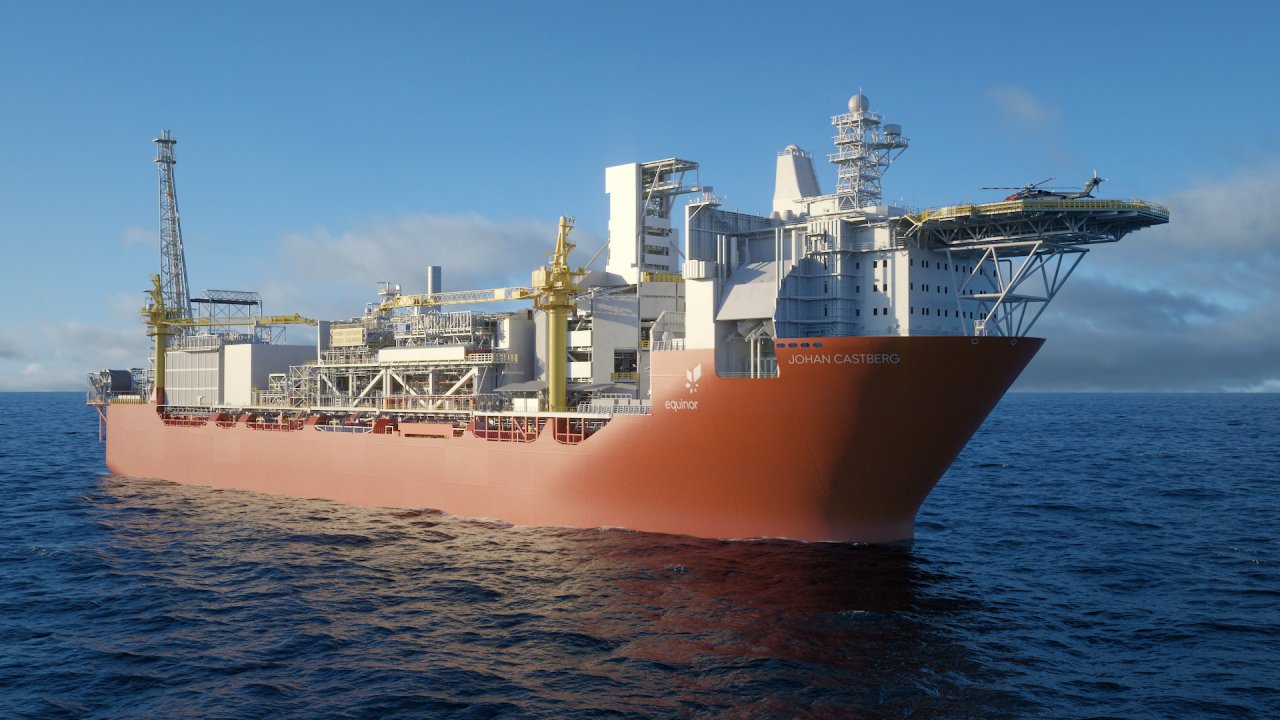
“We are preparing a plan with specific actions to follow up the findings and we will share our experience,” says Tungesvik.
The investigation team has studied the causes of the deviations in welding quality in the period from January 2017 to October 2019. Based on this work the team recommends Equinor to improve:
- the prequalification process for new suppliers
- the practice for follow-up at construction sites, including risk management
- the recruitment process for follow-up teams and team composition
Extensive control and improvement
When Equinor in the summer of 2019 cross-checked Sembcorp’s ultrasonic inspection of welds in the moonpool area of the hull by using own personnel, they discovered a higher failure rate than reported. It was then decided to cross-check all assembly welds. Unusually high failure rates in fabrication welds were revealed later.
“We have therefore reassessed all structural welds on the hull. This is a very demanding job as the hull has already been built, however safety comes first. The vessel must meet the requirements incorporated in the plan for development and operation (PDO) and obtain a DNV class certificate before sailing to the field,” says Tungesvik.
A reassessment of all structural welds has been made and extensive cross-checking is being carried out by use of non-destructive testing (NDT), including ultrasound.
“Equinor should have discovered the extent of welding defects earlier, however the hull is still in dock, allowing us to repair the defects before it is launched,” says Tungesvik.
The hull for the Johan Castberg production vessel is scheduled to be transported to Stord on board the Boka Vanguard heavy-lift vessel late 2021, however the Covid-19 pandemic still adds uncertainty to all schedules.