Kawasaki Heavy Industries, Ltd. announced today its obtainment of approval in principle (AiP) from Nippon Kaiji Kyokai (ClassNK) for a cargo containment system (CCS) offering the world's largest capacity (40,000 m3 class per tank), developed for use on a large liquefied hydrogen carrier.
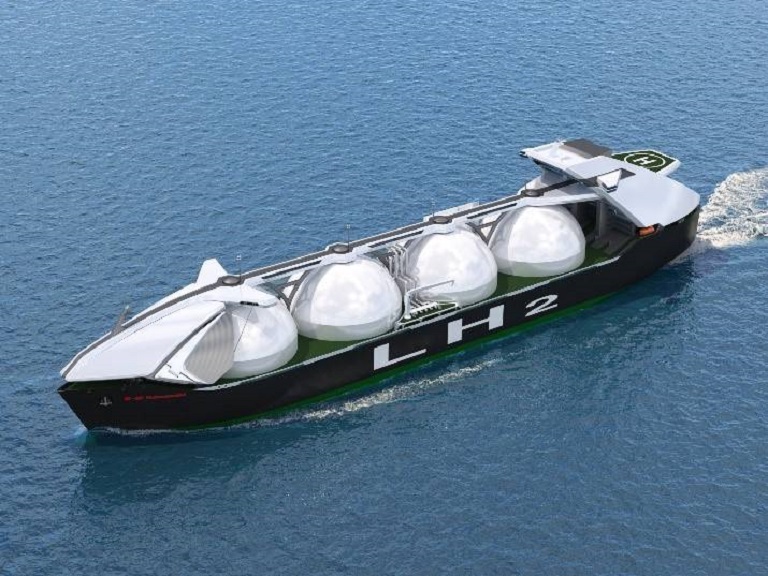
The CCS for which the AiP was obtained is designed to contain cryogenic liquefied hydrogen, reduced to a temperature of –253°C and one eight-hundredth its initial volume, for shipping by sea in large amounts. This containment system has the largest capacity of its kind worldwide used in liquefied hydrogen marine transport. The CCS was developed using design, construction and safety technologies fostered through building of the SUISO FRONTIER,*1 a pioneering liquefied hydrogen carrier built by Kawasaki that boasts a 1,250 m3 carrying capacity. In addition, the CCS utilizes a new type of insulation structure.
The recently obtained AiP was issued by ClassNK following examinations to confirm that the CCS satisfies the IGC Code*2 and the International Maritime Organization (IMO) Interim Recommendations for Carriage of Liquefied Hydrogen in Bulk,*3 and also clears class regulations as well as a risk assessment based on Hazard Identification Study (HAZID)*4 methods.
The main features of the CCS are as follows:
- Enables transportation of cryogenic liquefied hydrogen in large amounts thanks to tank capacity on par with tanks used on large liquefied natural gas (LNG) carriers
- Utilizes an independent, self-supporting design with a structure capable of responding flexibly to thermal contraction that occurs when loading cryogenic liquefied hydrogen
- Features a newly developed, high-performance heat insulation system that mitigates boil-off gas (BOG) which occurs in response to heat ingress
- Designed to effectively utilize BOG as fuel to power the ship, thus contributing to reduced CO2 emissions from liquefied hydrogen transport operations
Kawasaki developed the CCS as part of a project with financial support from NEDO,*5 and the Company is currently developing a large, 160,000 m3 liquefied hydrogen carrier using four CCS tanks, which is scheduled to start commercial operations by the middle of the 2020s. Amid global calls for the early achievement of carbon neutrality targets, Kawasaki is striving to achieve large-volume transport of liquefied hydrogen—for which demand is expected to grow as a clean energy source—in order to promote the use of hydrogen energy and help achieve decarbonization, working as one for the good of the planet.
Overview of the CCS
Tank type | Independent tank |
Diameter | Approx. 43 m |
Capacity | Approx. 40,000 m3 |
(*1) Constructed by Kawasaki as a member of the CO2-free Hydrogen Energy Supply-chain Technology Research Association (HySTRA; website: http://www.hystra.or.jp/en/ ), as part of the Demonstration Project for Establishment of Mass Hydrogen Marine Transportation Supply Chain Derived from Unused Brown Coal by the New Energy and Industrial Technology Development Organization (NEDO).
(*2) International Code for the Construction and Equipment of Ships Carrying Liquefied Gases in Bulk. A set of international regulations governing the constructions and equipment of such ships. All ships that carry liquefied gases and that were built in or after 1986 are forced to adhere to the code, and ClassNK incorporates the code as part of its Rules and Guidance for the Survey and Construction of Steel Ships.
(*3) Provisional recommendations adopted by the IMO for bulk transport of liquefied hydrogen.
(*4) Method of assessing risk, which is determined by experts based on the frequency with which potential hazards in a system arise, and aimed at identifying ways to minimize that frequency.
(*5) NEDO Technology Development Project for Building a Hydrogen-based Society / Technology Development Project for Large-Scale Utilization of Hydrogen / Project for Enlargement of Liquefied Hydrogen Cargo Tank Facilities and Development of Unloading Terminal Equipment.