In a world-first, Mitsui O.S.K. Lines (MOL) will bring a new type of hard sail equipped bulker to Newcastle, Australia later this year.
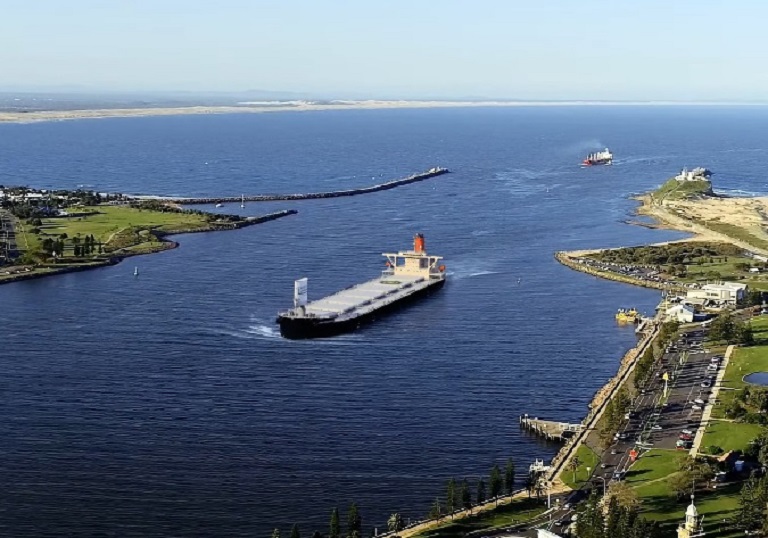
GHG savings
The single sail will produce enough propulsive force to save 5% of greenhouse gas emissions on the Japan-Australia route. However, the company notes that, in future, the multiple copies of the sail could be installed on a single ships and in a variety of different configurations. Larger ships with flat decks – such as the larger bulkers and tankers – could be especially suitable for the new sail type. MOL also notes that the system could, in future, also be installed on ships that are running on non-fossil fuels.
Bulkers and tankers are particularly suitable for wind assisted propulsion as wind systems on such vessels are much less likely to interfere with cargo operations when compared with other ship types. Bulkers and tankers also typically do not have high-speed requirements. Whereas a fully-laden containership will travel at about 25 knots (approx 46 km/h) a large fully laden bulker will more likely be travelling at about 10 knots (about 18.5 km/h). Some types of ships, such as large car carriers, are generally thought to be unsuited to sail technology as they already have a very high freeboard and, as such, already experience strong wind-force.
Hard sail
The hard sail system is called the “Wind Challenger”. It started life back in 2009 as a joint industry / academic project led by the University of Tokyo. In January 2018, MOL and Oshima Shipbuilding took over the plan and, in October 2019, Approval in Principle was granted by Class NK of Japan for the hard sail system.
The Wind Challenger system (in its first iteration) is installed near the prow of a bulker. It consists (in the first iteration) of four tiers of 15 metres wide by 20 metres high that are assembled on top of each other. However, the system at full extension will be 54m tall.
The biggest of the tiers is at the top and the smallest is at the bottom, which means that the sail-system can be made to telescopically extend or contract at will. So, if the wind is too strong, or if the seas are too rough, the system can be made to contract and it can also be rotated to provide maximum protection against damage. Similarly, when a ship is entering or leaving port, the system can be reduced in size so as to enable ease of navigation.
The sail is made of lightweight, strong, glass-fibre-reinforced plastic. This material enables easy control of thrust and load while “dramatically improving safety”, according to MOL, which adds that this is the first time that this particular fibre reinforced plastic has been used on large merchant ships.
The system will monitor sail and other environmental data, such as wind and wave) to optimise propulsion. Meanwhile, the ship will also sail more favourable routes, taking advantage of such phenomena as ocean currents, to maximise efficiency.
MOL set out its plan to achieve net zero GHG emissions by 2050 through concerted group-wide efforts in its MOL Group Environmental Vision 2.1. The company states it will contribute to reduce GHG emissions from society at large, and realize a low-carbon and decarbonized society by proactively participating not only in this project, but also by establishing clean energy supply chains. It states that it will “move assertively to promote wind-related businesses including the Wind Challenger-developed hard sail”.
Particulars
The first Wind Challenger-equipped ship will also be named “Wind Challenger”. It will have a deadweight of approximately 98,9000 tonnes and seven hatches/ holds. Hatch 1 (at the prow) will be 13.35m x 21.00 metres and the others will be 18.69 metres x 21 metres. Length between perpendiculars will be 321 metres and it will have a breadth of 43 metres, a depth of 20 metres and a designed draft of 12.8 metres.